Find Best Food Service Distribution Software for Your Business
We help you find the right Food Service Distribution Software for your business.
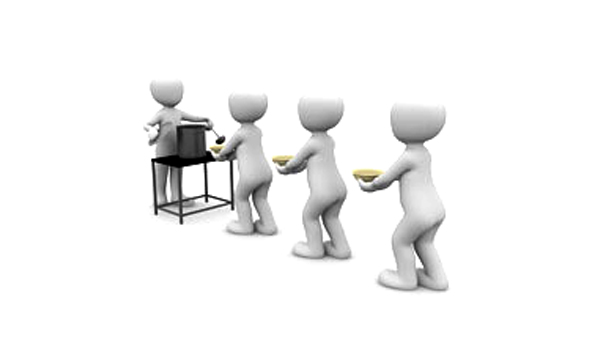
Food Service Distribution Software:
Food Service Distribution Software is a software that is used by food distributors and wholesalers to automate resource planning, distribution and order fulfillment activities.
Users can schedule, track, and manage inventory related to food storage and distribution by using Food Service Distribution Software. The everyday challenges for food and beverage distributors and wholesalers such as changing fuel prices, potential food spoilage, safety regulations can be addressed by using this software. It helps the importer or exporter, brokerage, or supplier as well as retailers and restaurants to get the right food products to the right places at the right times, while reducing waste. The user will be able to handle frequent changes in costs and customer demand by food safety and quick delivery provided by the software.
Features and Benefits of Food Service Distribution Software:
The Food Service Distribution Software has several features that can benefit the user in many ways to grow their business. Some of these include:
- Quality control, compliance, traceability, inventory management, warehouse operations, purchasing, sales, financials and more can be effectively managed from a single integrated system, built for your industry needs.
- Your performance can be optimized and company growth can be enhanced by identifying opportunities and the area to improve.
- Shipments can be planned, customers can be managed, and well-documented records of food orders can be maintained for food service distribution companies.
- It also helps to process orders, manage payments, track deliveries, and manage inventory.
- Analytics reports can be produced to use in sales processes and performance evaluation is one of the most common features of the software.
- Sales effectiveness can be increased by analyzing performance, profits, and market prices.
- Inventory can be allocated to orders on a first expire first out basis to proactively move products before expiration.
- Sales across your organization can be maximized with visibility into opportunities and pipeline.
- Paperwork can be reduced with Electronic Data Interchange (EDI) to automate order processing.
- Efficiency can be improved with repeat order customer templates.
- Complex pricing such as contract pricing, volume discounts, trade promotions and rebates can be managed easily.
- Your web presence can be increased with B2B and B2C e-commerce shopping cart.
- Inventory can be controlled and streamlined with tools to improve forecasting and planning. You can match supply with customer demand.
- Customer and supplier requirements can be responded quickly with seamless data interchange between external trading partners and value added networks.
- Visibility across the supply chain can be gained by tracking materials from supply chain source through final destination while taking ownership as soon as the voyage is departed.
- All aspects of inventory management can be controlled with bi-directional lot traceability, integrated quality control, and shelf life and expiration date tracking.
- Purchasing decisions can be optimized by verifying integrate point of sale (POS) data, customer forecasts, historical sales trends, seasonality and supplier lead times.
- The time can be accelerated to completion of your product recalls.
- Your traceability system can be improved by continually testing.
- You can mitigate the reputation risks associated with recall and remain compliant by meeting regulatory requirements.
- A full product recall can be performed quickly and efficiently by rapidly identifying and retrieving potentially defective goods from customers using the Product Recall system of organization.
- Forecast errors can be minimized by fine tuning the balance between supply and demand.
- Automated processes and actions for authorizing and tracking customer returns, warranty claims and complaints can be streamlined to manage and control the Return Process.
- Multiple locations for different product types, quality and frozen goods can be managed with automated processing with barcoding.
- Greater visibility, compliance and quality control can be enabled in the procurement and supplier selection process.