Find Best Job Shop Software for Your Business
We help you find the right Job Shop Software for your business.
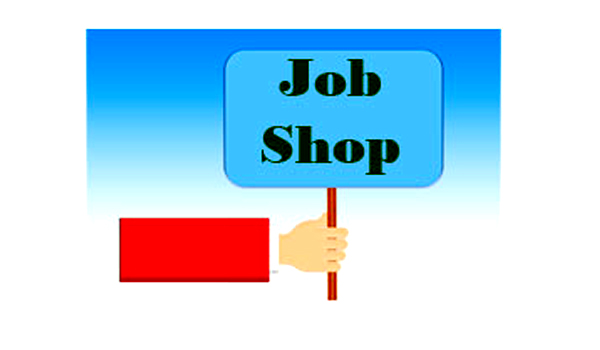
Browse Popular Job Shop Software
Up-to-date listing of Job Shop Software to assist you throughout your software selection and purchase journey.
Job Shop Software:
Job Shop Software is a light version of ERP systems that is used by small manufacturers and single owner operators to manage production activities without investing in expensive ERP systems.
Activities such as sales and purchasing, inventory management, light manufacturing, and sometimes equipment and accounting can be done by using this software. Job Shop Software can be used by all employees, but it is particularly beneficial to production and inventory management teams.
Features and Benefits of Job Shop Software:
The Job Shop Software has several features that can benefit the user in many ways to grow their business. Some of these include:
- Manufacturing and assembly features such as BOM (bills of materials) can be provided.
- Workflows can be included to assign employees or teams to various activities.
- Work orders can be created based on customer demand.
- The inventory of components required for production can be managed.
- Production costs per operation, work order, team, or customer can be tracked.
- The capabilities of repetitive, custom, quick-turn and mixed mode operations can be optimized.
- Features like Accounting, Business Analytics, CRM, EDI, COM's Bar coding, HR, Inventory Control, Invoicing, Quality Control and Inspection, Repair and Maintenance, RFQ/Quoting, Sales and purchase Order Processing, Time Clock, and Work Order Scheduling and Reporting can be streamlined for maximum speed, efficiency, accuracy and control all in real time.
- Kiosk Data Collection and Whiteboard Scheduling modules can be offered with drag and drop scheduling.
- It contains customer and vendor centers and an executive management overview to ensure each use and access to real time data updates.
- The visibility required to optimize your processes can be provided, your uptime can be increased, and future orders can be analyzed and planned by the real-time tracking, global OEE and traceability offered by the software.
- All tracking and traceability information can be collected in one place in real time. You will be prepared for ISO 9001 and ISO TS 16949 audits by simply generating the report through he built-in Quality Module.
- Bottlenecks can be located, uncover where raw materials are being wasted, days can be predicted and prevented, and it can be ensured that the quality requirements are met with easy to use manufacturing execution system.
- The real time information collected from the shop floor can be fed to the dashboards for generating reports through mobile devices. So, your entire production flow including orders, workers, materials, machines, maintenance, waste, time, costs can be tracked and analyzed in real time.
- Full visibility into your resources, from workers to machines including Who is doing what, where, when and how can be provided through visual scheduler. So, your operations can be effectively planned and scheduled to balance the workload, align your shifts and meet your production targets.
- The availability of all your goods, from raw materials to finished products can be managed through its Inventory Module. you will be able to track your consumption in real time, improve your purchasing process, and maximize your warehouse space by adding Bill of Materials (BOM) and Product Trees.
- As all the reports and records you need can be provided in real time, you can be ready for an audit at any time. you will empower your workers with the necessary information to perform at their best by sharing a Quality Policy, work instructions and Quality and Safety Checklists with your team.